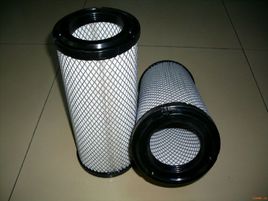
Combined dedusting
catalog
-
1. Classification of combined dedusting products -
2. Common application of combined dedusting -
3. Development history of combined dedusting -
4. Business opportunity of combined dedusting -
5. Combined dedusting brand -
6. Combined dust removal news -
7. Combined dedusting enterprise -
8. Combined dedusting quotation -
9. Combined dust removal atlas
1. Classification of combined dedusting
2. Common application of combined dedusting
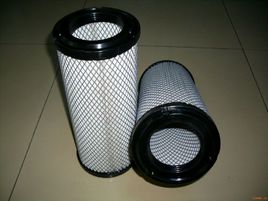
3. Development history of combined dedusting
4. Business opportunity of combined dedusting
5. Combined dedusting brand
6. Combined dust removal news
-
Floor enterprises will be reborn through "combined marketing" In recent years, with the intensification of industry reshuffle, the survival of the fittest has promoted the development of the flooring industry to a certain extent, but at the same time, the surge of internal and external pressure has also made the flooring enterprises enter a difficult situation. [Detailed] -
Flooring enterprises may go out of the low tide through combined marketing In recent years, with the intensification of industry reshuffle, the survival of the fittest has promoted the development of the flooring industry to a certain extent, but at the same time, the surge of internal and external pressure has also made the flooring enterprises enter a difficult situation [Detailed]
7. Combined dedusting enterprise
8. Combined dedusting quotation
9. Combined dust removal atlas
Related information
-
Wallpaper dealers take retreat as a step forward and combine operation to resist the cold winter -
Features of SMC combined water tank -
How to maintain the combined air conditioner -
Combined operation becomes a new development mode of wallpaper industry -
The transformation of cabinet hardware industry can adopt the "polymerization" development route -
Competitive means for combined operation to become a wooden door dealer in second tier cities