Networking and synchronization with CNC machine tools
hyperMILL® CONNECTED Machining
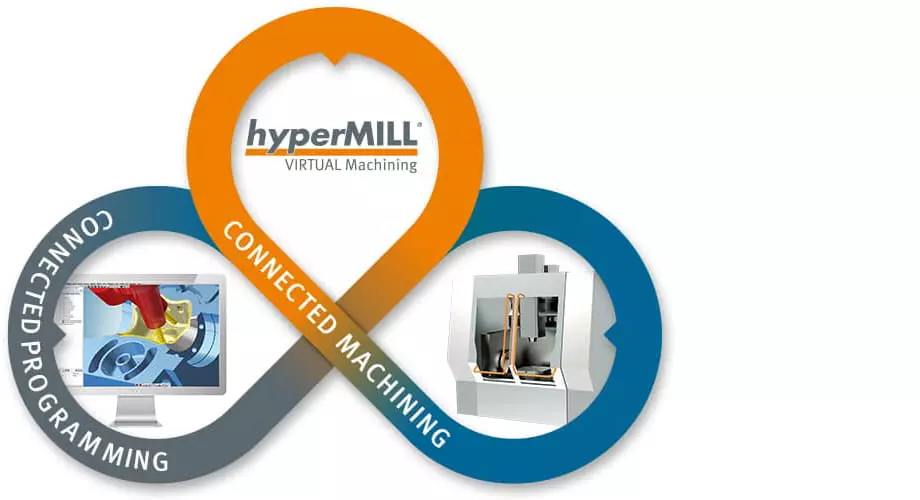
function
Transfer to controller
-
Tool information -
NC program
read
-
Tool and zero information -
Machine parameters -
Sensor data
inspect
-
Machine tool remote control
Ensure that the whole process of execution is very safe
Comprehensive process control