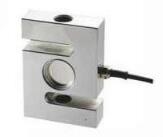
The tension sensor is capable of measuring the tension or tension of an object TPS2051BDGNR Sensor. They are widely used in industrial automation, aerospace, automotive engineering and other fields to measure and monitor the tensile force of objects. This paper will introduce the basic structure, advantages and disadvantages, working principle, application, structure classification, wiring method, installation, use and development history of the tension sensor.
1、 Basic structure
The basic structure of tension sensor mainly includes elastic element, measuring circuit and shell. Elastic element is the core part of tension sensor, which is generally made of metal materials, such as steel, aluminum, etc. The shape of elastic elements can be curved beams, spiral springs, etc., and their selection depends on the specific requirements of the application. The measuring circuit is the part that converts the deformation of elastic elements into electrical signals. It is generally composed of resistance strain gauge, bridge circuit and amplification circuit. The housing is used to protect elastic elements and measuring circuits, and also plays the role of fixing and connecting sensors.
2、 Advantages and disadvantages
1. Advantages:
(1) Wide measuring range: the tension sensor can measure the tension from several to tens of thousands of cows, with a wide range of applications.
(2) High precision: the measurement accuracy of the tension sensor is high, which can reach 0.1% or higher.
(3) High reliability: because of its simple structure and no vulnerable parts, it has high reliability and long service life.
(4) Easy to install and use: The tension sensor is usually connected by thread, which is easy to install and use.
(5) Fast response speed: the tension sensor has fast response speed, and can monitor the force in real time.
2. Disadvantages:
(1) High price: Due to the complex manufacturing process and high material cost of the tension sensor, the price is relatively high.
(2) Affected by environment: the tension sensor is sensitive to environmental temperature, humidity and other factors, which may affect the measurement accuracy.
(3) Vulnerable to external force interference: because the deformation of elastic elements is affected by external force, they are vulnerable to external force interference, which may lead to measurement errors.
3、 Operating principle
The working principle of the tension sensor is based on Hooke's Law, that is, the tension on the object is proportional to the deformation of its elastic element. When the object is under tension, the elastic element will have a certain deformation. By measuring this deformation, the tension of the object can be obtained. Generally, resistance strain gauge is used as elastic element, and its resistance will change with deformation. The measuring circuit determines the pulling force on the object by measuring the change of resistance value.
4、 Application
Tension sensors are widely used in various fields. In industrial automation, they are used to measure and control the tension of objects, such as conveyor belts, cranes, etc. In aerospace, they are used to measure the stress of aircraft structures. In automotive engineering, they are used to measure the braking force and engine output force of vehicles.
5、 Structural classification
1. Resistance strain type: resistance strain type tension sensor is the most common type. Based on the resistance strain effect, it indirectly measures the force by measuring the resistance value change caused by the force on the object. The resistance strain gauge is usually pasted or welded on the force measuring element. When the force acts on the force measuring element, it will lead to the deformation of the resistance strain gauge, thus causing the change of resistance value.
2. Capacitive type: the capacitive tension sensor measures the force by the change of capacitance. It is usually composed of two metal electrodes. When the force acts on the capacitive sensor, the capacitance value between the electrodes will change, thus reflecting the force.
3. Inductive type: inductive tension sensor mainly depends on the change of inductance to measure the force. It is usually composed of coil and iron core. When the force acts on the inductance sensor, the inductance value of the coil will change, reflecting the magnitude of the force.
4. Photoelectric type: Photoelectric tension sensor uses the transmission of light to measure the force. It is usually composed of light source, photodiode and photoresist. When the force acts on the sensor, the light transmission path will change, which will affect the light signal intensity received by the photodiode, thus reflecting the force.
6、 Wiring method
The wiring method of the tension sensor is usually determined according to the interface type of the sensor. Common wiring methods include:
1. Electric bridge connection: resistance strain type tension sensor is usually connected by electric bridge circuit. The bridge circuit is usually composed of four resistors, including two resistance strain gauges and two compensation resistors. By adjusting the resistance value of the compensation resistor, the output voltage can be proportional to the force.
2. Capacitive connection: capacitive tension sensor usually needs to be connected to the measuring circuit for signal processing. When wiring, it is necessary to connect the capacitive plate of the sensor to the measuring circuit, and carry out signal amplification and filtering processing through the appropriate circuit.
3. Inductive connection: Inductive tension sensor usually needs to be connected to the measuring circuit for signal processing. When wiring, the coil of the sensor needs to be connected to the measuring circuit, and the signal is amplified and filtered through the appropriate circuit.
4. Photoelectric connection: Photoelectric tension sensors usually need to be connected to photoresistors or photodiodes for signal detection. When wiring, it is necessary to connect the light source and photosensitive element of the sensor with the measuring circuit, and detect the signal through the photoelectric element.
7、 Installation and use
The installation and use of tension sensor mainly include the following steps:
1. Select the appropriate tension sensor: select the appropriate tension sensor according to the measured tension range, working environment and needs. Common tension sensors include strain type tension sensor, capacitive tension sensor and resistance type tension sensor.
2. Installing sensor: install the tension sensor on the object that needs to measure the tension. During installation, it is necessary to ensure the close contact between the sensor and the object to ensure that the sensor can accurately sense the tension.
3. Connecting circuit: connect the output terminal of the sensor with the corresponding circuit. Generally, the weak electrical signal output by the sensor is amplified through the amplifier and other circuits, and converted into available voltage or current signals.
4. Calibrate the sensor: before using the tension sensor, it needs to be calibrated to ensure the accuracy of the measurement results. The aim of calibration is to determine the linear relationship between the sensor output and the actual tension, and to correct any nonlinear errors.
5. Tension measurement: when using a tension sensor to measure the tension, it is necessary to apply tension to the measured object and read the electrical signal output by the sensor. According to the sensitivity and range of the sensor, the electrical signal can be converted into the corresponding tension value.
8、 Development history
The development of tension sensors can be traced back to the 19th century. The earliest tension sensor is based on mechanical principle, which indirectly measures the force by measuring the deformation of spring or bending bar. With the development of electronic technology, resistance, capacitance, inductance and other electronic tension sensors begin to appear, greatly improving the measurement accuracy and sensitivity.
After the 1960s, with the progress of semiconductor technology, microelectronic tension sensors began to appear. This kind of sensor adopts micro chip and micro machining technology, which makes the sensor smaller, faster response and higher reliability.
In recent years, with the development of Internet of Things and artificial intelligence technology, tension sensors have also begun to connect and integrate with other sensors and intelligent devices to achieve more functions and applications. For example, the combination of tension sensor and wireless communication technology can realize remote monitoring and control; The trend analysis and prediction of force can be realized by combining the tension sensor with the data analysis algorithm.