When implementing industrial automation solutions, especially when Siemens S7-1200/1500 series is involved PLC A common problem in the integration of is to ensure the compatibility between different communication protocols. In this case, we are faced with the need to connect these PLCs with inverter equipment that supports EtherCAT communication function. Siemens PLC usually uses PROFINET real-time Ethernet communication protocol to realize fast and reliable data exchange. In order to realize seamless interface with the inverter equipment based on EtherCAT, it is necessary to convert these two different real-time Ethernet protocols through Wuxi Netsun EtherCAT to Profinet gateway.
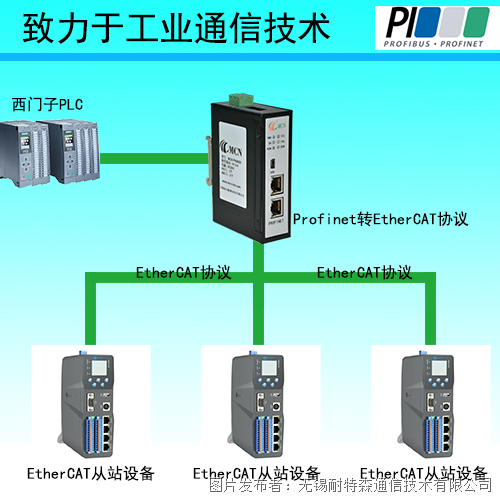
In this context, our EtherCAT to Profinet gateway plays a crucial role. It not only provides a quick and practical means for the above communication protocol conversion, but also the EtherCAT to Profinet gateway is designed to support the role of both master and slave, thus realizing data mapping and interaction between two independent networks. We need to add the GSD file of EtherCAT to Profinet gateway to the project. This step is critical to ensure correct equipment identification and configuration. We found the EtherCAT to Profinet gateway module in the control engineer workstation and started its configuration settings.
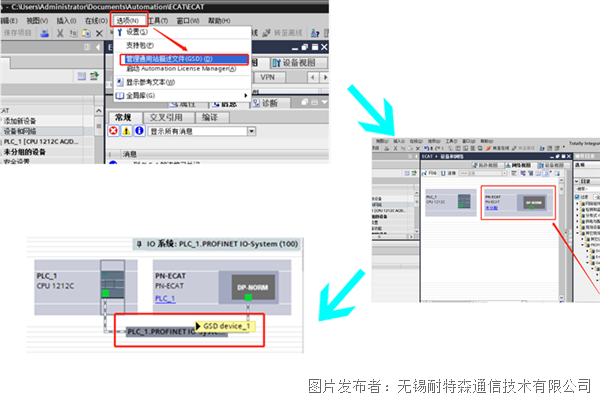
The IP field and equipment name of EtherCAT to Profinet gateway must be configured. This is to ensure the accurate positioning and identification of equipment in the network. We need to set the length of input and output bytes of EtherCAT to Profinet gateway to ensure the accuracy and efficiency of data exchange. Through this professional configuration process, we can ensure the effective connection between Siemens PLC and inverter equipment with EtherCAT communication function, thus optimizing the operation efficiency of the entire automation system. In the process of building the industrial automation system, the following steps are the key to realizing the configuration of EtherCAT to Profinet gateway based on PROFINET protocol.
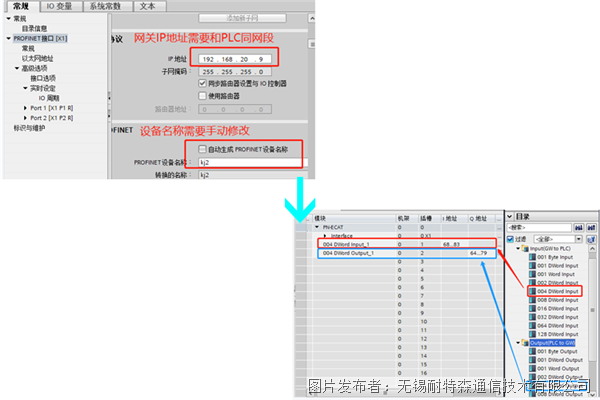
Download the configuration to the PLC, and download the pre designed control logic and parameter settings to the PLC equipment to ensure that the system is executed according to the predetermined operation process. Start EtherCAT to Profinet gateway configuration software to set ECAT: through special configuration software, set EtherCAT technology in detail to achieve efficient real-time data transmission and accurate equipment synchronization.
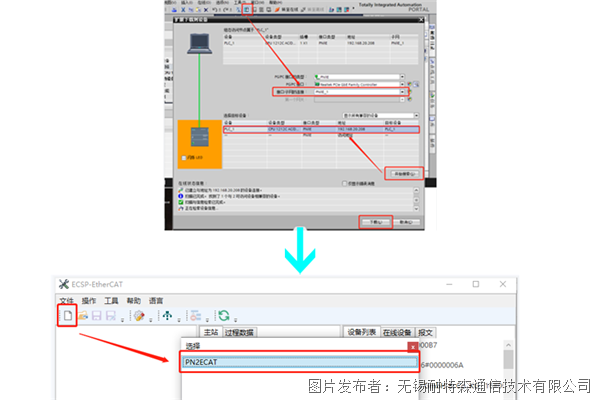
Create a new project in the configuration software, and select the corresponding functions to combine the Profinet protocol with EtherCAT technology. Configure the IP address and device name of the software to ensure that they are consistent with the blog. In order to achieve seamless connection of network communication, it is necessary to ensure that the IP address and device name in the software match the corresponding information in the control system. Browse the device directory provided by the configuration software, locate and select the target device to be controlled.
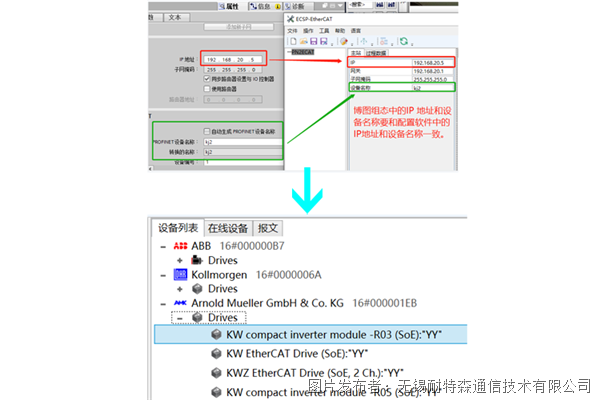
Configure the parameters of the slave equipment, add the parameter items of the process data object, and add the required PDOs parameter items. These parameter items have been preset in the configuration file, so that they can be directly downloaded to the EtherCAT to Profinet gateway, and execute the running command after the configuration is completed.
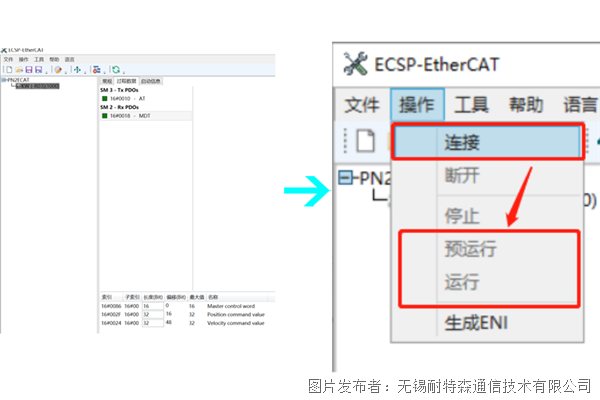
Directly read and write the corresponding IQ address: in this case, The EtherCAT to Profinet module acts as a bridge between the inverter and Siemens PLC. It maps the data through the configuration software to realize the rapid control of S7-1200 PLC over the inverter through the PROFINET protocol. Through the above professional configuration steps, the EtherCAT to Profinet network configuration can be effectively realized, providing an efficient and reliable control scheme for the industrial automation system.